How to Create a Team Leader Based Organization
Oct 22, 2015 | Posted by Ben Thompson
Teamwork is a Foundation of the Toyota Production System
What is the development framework to develop a “team leader” based organization?
Roles & Responsibilities of:
- Production Manager – Responsible for overall performance of a Manufacturing Unit
- Supervisor – Responsible for about 35 people; Responsible for People, Equipment and Processes
- Team Leader – leading a team of 6 to 9 employees; Responsible for daily production results; Responsible for sustaining and implementing manufacturing processes; Responsible for Continuous Improvement activities; Team development – not for disciplinary issues
Manager’s Roles & Responsibilities:
- Provide and secure all resources necessary to achieve company goals and objectives
- Assure that all company rules, policies and standards, are followed and complied
- Provide safe and healthy work environment for all employees
- Make sure that for everything we do there is a well defined standard procedure, which is followed by all employees
- Push the decision making process to the lowest possible level in your organization
- Initiate problem solving and improvement activities
Supervisors Roles & Responsibilities:
- People Responsibility
- Administrative: policies, attendance, corrective actions, manpower and vacation planning
- People development, cross-training and team morale
- Group safety performance
- Coordinate work with other departments – Overtime
- Help cover TL absence
- Coordinate support from outside groups
- Continuous Improvement Activities – Quality Circles
- Process Responsibility
- Report and track daily production results
- Shift to shift coordination
- Monthly production planning
- Operating budget and cost control
- Cost reduction activities and process improvement projects : productivity, quality, ergonomics, etc.
- Coordinate major maintenance activities
- Confirm routine quality and TL checks
- Supervisor Skill Requirements
- Working knowledge of all manufacturing processes, equipment, parts and components in his/her area of responsibility
- Knowledge of company’s policies, rules and regulations applying to his/her area of responsibility
- Knowledge of all health and safety, quality and labour standards applying to his/her area of responsibility
- Leadership skills, facilitation skills, problem solving skills, management skills and planning skills
- Understanding of principles of TPS / continuous improvement
Team Leader’s Roles & Responsibilities:
- People Responsibility
- Respond to T/L calls by operators
- Assign work to operators, cover absenteeism and support employees when necessary
- Conduct training and cross-training
- Assure that Standardized Work is followed
- Facilitate small group activities
- Initiate and work on Continuous Improvement projects
- Process Responsibility
- Process start-up and control
- Meet production goals – achieve daily production results
- Assure that all equipment and machinery is operational and in good working order
- Confirm quality – conduct routine checks
- Assist in set-ups and changeovers when necessary
- Insure parts and materials are supplied to operators
- Issue Work orders for quick maintenance
- Collect data and completed required reports
- Team Leader Skill Requirements
- Working knowledge of all “Jobs” in his/her area of responsibility – ability to perform any job in the area
- Understanding of all manufacturing processes, equipment and procedures in his/her area
- Demonstrated ability to train people Leadership, problem solving and analytical skills
- Knowledge of company’s policies, rules and regulations applying to his/her area of responsibility
- Understanding of principles of TPS / continuous improvement
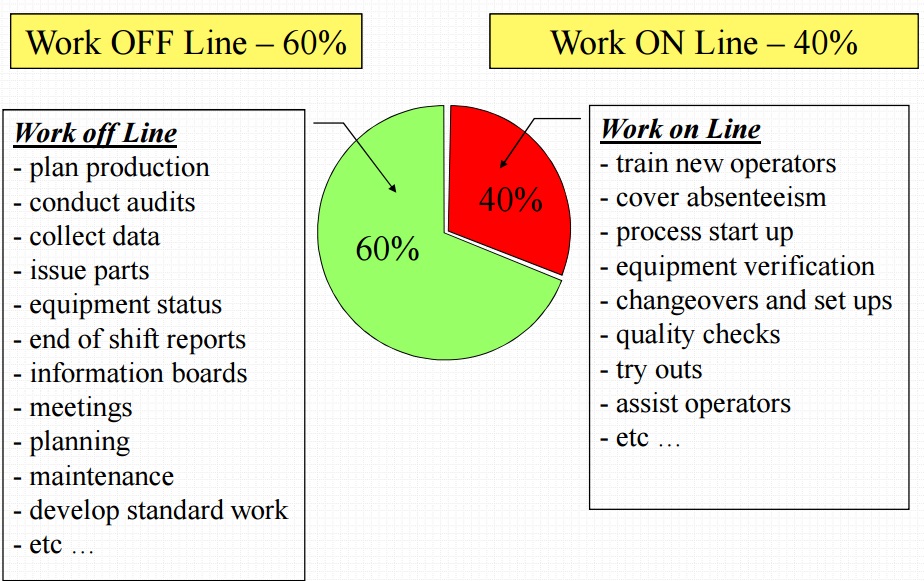
What does your team-leader based organization look like?
Marek
marek@truenorththinking.ca
416-235-2531
Learn Four Strategies To Start Improving Any Area Of Your Business